Tungsten Carbide vs. Traditional Metals: Which One Should You Choose?
- Share
- Issue Time
- Dec 4,2024
Summary
When it comes to selecting materials for various applications, the debate between Tungsten Carbide and Traditional Metals is significant. At Dongcheng, we understand that making the right choice can impact durability, performance, and overall satisfaction. In this comprehensive guide, we will explore the differences, advantages, and applications of these two material categories to help you make an informed decision.
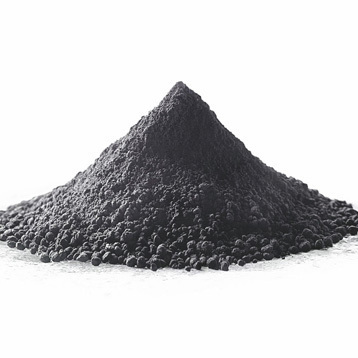
Tungsten Carbide vs. Traditional Metals: Which One Should You Choose?
When it comes to selecting materials for various applications, the debate between Tungsten Carbide and Traditional Metals is significant. At Dongcheng, we understand that making the right choice can impact durability, performance, and overall satisfaction. In this comprehensive guide, we will explore the differences, advantages, and applications of these two material categories to help you make an informed decision.
Understanding Tungsten Carbide
Tungsten Carbide is a high-performance composite material made from tungsten and carbon. Known for its exceptional hardness and resistance to wear, it is frequently used in industries that demand durability and precision.
Properties of Tungsten Carbide
1.Extreme Hardness: Tungsten Carbide ranks around 9 on the Mohs hardness scale, second only to diamond. This makes it incredibly resistant to scratches and abrasions.
2.High Density: With a density that is more than twice that of steel, Tungsten Carbide provides substantial weight and stability in applications.
3.Wear Resistance: The material's resistance to wear and tear makes it ideal for cutting tools and industrial machinery components, extending their life span significantly.
4.Thermal Stability: Tungsten Carbide maintains its properties even at high temperatures, making it suitable for applications where heat is a concern.
5.Corrosion Resistance: Unlike many traditional metals, Tungsten Carbide is less susceptible to corrosion, enhancing its longevity in various environments.
6.Exploring Traditional Metals
Traditional metals, such as steel, aluminum, and copper, have been used for centuries in various applications due to their availability and versatility. Each metal has unique characteristics that make it suitable for specific uses.
Properties of Traditional Metals
1.Steel: Known for its strength and versatility, steel is widely used in construction and manufacturing. However, it may be prone to rust if not properly treated.
2.Aluminum: Lightweight and corrosion-resistant, aluminum is often used in the aerospace and automotive industries. However, it may not withstand high wear conditions as effectively as Tungsten Carbide.
3.Copper: Renowned for its excellent conductivity, copper is primarily used in electrical applications. However, it is softer than Tungsten Carbide and can wear out more quickly.
4.Comparative Analysis: Tungsten Carbide vs. Traditional Metals
Durability and Longevity
When comparing durability, Tungsten Carbide outshines traditional metals. Its extreme hardness ensures that tools and components made from this material last significantly longer than those made from steel or aluminum. For instance, in manufacturing environments, Tungsten Carbide cutting tools can last up to 10 times longer than their steel counterparts, reducing downtime and increasing productivity.
Cost Considerations
While Tungsten Carbide is generally more expensive upfront than traditional metals, its longevity and reduced maintenance costs can lead to significant savings over time. Companies investing in Tungsten Carbide tools may find that the initial investment pays off through decreased replacement frequency and lower operational costs.
Weight and Application Suitability
In applications where weight is a critical factor, traditional metals like aluminum may be preferred. However, for heavy-duty applications that require strength and durability, Tungsten Carbide is the superior choice. For instance, in the mining industry, Tungsten Carbide bits are used for drilling due to their ability to withstand extreme conditions.
Performance Under Stress
Tungsten Carbide exhibits exceptional performance under stress, making it ideal for high-impact applications. Traditional metals may deform or fail under similar conditions, leading to potential failures in critical components.
Applications of Tungsten Carbide
Industrial Tools
Tungsten Carbide is a staple in manufacturing and industrial applications. Tools such as drills, end mills, and cutting inserts are often made from Tungsten Carbide due to their durability and effectiveness in high-wear environments.
Jewelry
In the realm of fashion, Tungsten Carbide has gained popularity for wedding bands and other jewelry. Its scratch-resistant properties and unique aesthetic appeal make it an attractive choice for consumers looking for lasting quality.
Mining and Drilling
The mining industry relies heavily on Tungsten Carbide for drilling and cutting tools. Its ability to withstand harsh conditions and resist wear makes it indispensable in this sector.
Applications of Traditional Metals
Construction
Steel continues to dominate the construction industry due to its strength and versatility. It is used in beams, reinforcements, and various structural components.
Automotive
Aluminum is widely used in the automotive industry for its lightweight properties, contributing to fuel efficiency without compromising safety.
Electrical Applications
Copper remains the go-to metal for electrical wiring due to its excellent conductivity, making it essential in the manufacturing of electrical components.
Making the Right Choice: Factors to Consider
When deciding between Tungsten Carbide and traditional metals, consider the following factors:
1.Application Requirements: Assess the specific demands of your project. For high-wear applications, Tungsten Carbide may be the better option.
2.Budget: While Tungsten Carbide has a higher initial cost, its longevity can translate to cost savings over time.
3.Weight Constraints: If weight is a critical factor, traditional metals may be more suitable for your needs.
4.Environmental Conditions: Consider the environmental factors your materials will face. Tungsten Carbide excels in harsh conditions compared to many traditional metals.
Conclusion
In conclusion, the choice between Tungsten Carbide and Traditional Metals ultimately depends on your specific needs and application requirements. At Dongcheng, we advocate for informed decision-making based on the unique properties and advantages of each material. Whether you prioritize durability, cost-effectiveness, or application suitability, understanding the strengths and weaknesses of Tungsten Carbide compared to traditional metals will empower you to make the best choice for your projects.
For more information about our range of Tungsten Carbide products and how they can benefit your applications, contact us today. Let Dongcheng help you achieve the performance and reliability your projects demand.
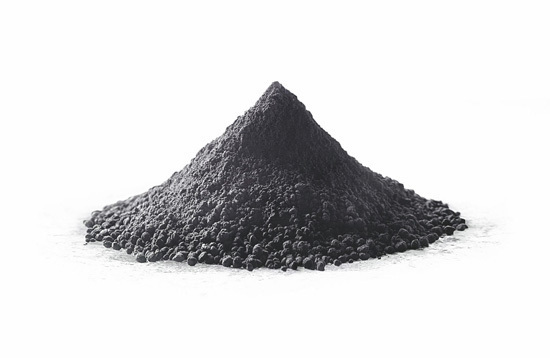