Tungsten Carbide Cutting Wheels vs. Traditional Wheels: Which Is Better?
- Share
- Issue Time
- Mar 12,2025
Summary
In the world of cutting tools, the selection of the right wheel can significantly impact the efficiency and quality of your work. Tungsten carbide cutting wheels and traditional wheels each have their unique advantages and disadvantages.
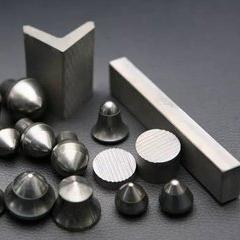
Tungsten Carbide Cutting Wheels vs. Traditional Wheels: Which Is Better?
Introduction
In the world of cutting tools, the selection of the right wheel can significantly impact the efficiency and quality of your work. Tungsten carbide cutting wheels and traditional wheels each have their unique advantages and disadvantages. At Dongcheng, we pride ourselves on offering top-quality cutting solutions, and understanding the differences between these two types of wheels is essential for optimizing your cutting tasks. This article delves into the characteristics, benefits, and applications of tungsten carbide cutting wheels compared to traditional wheels, helping you make an informed decision for your projects.
What Are Tungsten Carbide Cutting Wheels?
Tungsten carbide cutting wheels are engineered from a robust composite of tungsten and carbon, resulting in a wheel that is not only hard but also highly resistant to wear and heat. These wheels are primarily designed for heavy-duty applications and are known for their exceptional durability and longevity.
Key Features of Tungsten Carbide Cutting Wheels
Exceptional Hardness: Tungsten carbide is one of the hardest materials available, making these wheels ideal for cutting through tough materials such as metals, ceramics, and composites.
Heat Resistance: The high melting point of tungsten carbide allows these wheels to perform efficiently even under extreme temperatures, reducing the risk of thermal damage during prolonged use.
Precision Cutting: Tungsten carbide wheels provide a clean and precise cut, minimizing material waste and enhancing the overall quality of the finished product.
What Are Traditional Wheels?
Traditional cutting wheels are typically made from aluminum oxide or silicon carbide. They have been a staple in various industries for decades due to their versatility and cost-effectiveness.
Key Features of Traditional Wheels
Affordability: Traditional wheels are generally less expensive than tungsten carbide options, making them an attractive choice for budget-conscious projects.
Versatility: These wheels can be used on a variety of materials, including wood, plastic, and softer metals, making them suitable for general-purpose applications.
Availability: Traditional wheels are widely available and come in numerous sizes and specifications, catering to various cutting needs.
Comparative Analysis: Tungsten Carbide vs. Traditional Wheels
Durability and Longevity
When it comes to durability, tungsten carbide cutting wheels outperform traditional wheels by a significant margin. The enhanced hardness of tungsten carbide means that these wheels can endure more rigorous cutting tasks without wearing down quickly. Traditional wheels, while effective for lighter applications, will require more frequent replacements, leading to increased costs over time.
Cutting Performance
Cutting Precision: Tungsten carbide wheels offer superior cutting precision compared to traditional wheels. The sharpness of the tungsten carbide edge allows for finer cuts, reducing the need for additional finishing work. This is particularly beneficial in industries where precision is paramount, such as aerospace and automotive manufacturing.
Speed and Efficiency: Tungsten carbide cutting wheels can achieve faster cutting speeds due to their hardness, which allows them to cut through materials more efficiently. In contrast, traditional wheels may slow down during tough cuts, leading to longer project timelines.
Heat Management
Heat generation during cutting can significantly affect performance. Tungsten carbide wheels are designed to dissipate heat effectively, which not only prolongs the wheel's lifespan but also minimizes the risk of warping the material being cut. Traditional wheels, on the other hand, may struggle with heat management, leading to reduced cutting efficiency and potential damage to both the wheel and the workpiece.
Material Compatibility
While tungsten carbide cutting wheels excel in cutting hard materials, traditional wheels have their place in softer applications. For users primarily working with wood, plastics, or non-ferrous metals, traditional wheels may suffice. However, for those tackling tougher materials, tungsten carbide is the clear winner.
Applications of Tungsten Carbide Cutting Wheels
Tungsten carbide cutting wheels are versatile tools suitable for a variety of applications, including:
Metal Fabrication: Ideal for cutting steel, aluminum, and other metals with precision and speed.
Aerospace and Automotive: Used for intricate cuts that require high precision and durability.
Construction: Perfect for cutting through hard materials like concrete and masonry.
Woodworking: Effective for detailed work on hardwoods and engineered materials.
Applications of Traditional Wheels
Traditional wheels serve well in applications such as:
General Maintenance: Suitable for light-duty tasks and routine maintenance work.
Woodworking: Effective for cutting softer woods and materials.
Craft and DIY Projects: Ideal for hobbyists and home projects where budget constraints are a concern.
Cost Considerations
While tungsten carbide cutting wheels may have a higher upfront cost compared to traditional wheels, the long-term savings associated with their durability and efficiency often outweigh the initial investment. Users can benefit from reduced replacement frequency and increased productivity, making tungsten carbide a more economical choice in the long run.
Conclusion
In the debate of tungsten carbide cutting wheels vs. traditional wheels, the choice ultimately depends on the specific needs of your project. For heavy-duty applications that require precision, durability, and efficiency, Dongcheng’s tungsten carbide cutting wheels are the clear choice. However, for lighter tasks and budget-friendly options, traditional wheels may suffice.
When making your decision, consider the materials you will be working with, the frequency of use, and the importance of precision in your projects. At Dongcheng, we are committed to providing you with the best cutting solutions tailored to your needs, ensuring that you achieve optimal results every time.
Invest in quality, invest in Dongcheng.
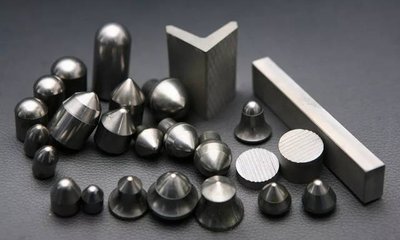