Maximize Your Cutting Efficiency: The Science Behind Tungsten Carbide Cutting Wheels
- Share
- Issue Time
- Mar 26,2025
Summary
In the world of precision cutting, tungsten carbide cutting wheels stand out as the premier choice for professionals and hobbyists alike. Renowned for their durability, sharpness, and efficiency, these cutting wheels are engineered to deliver superior performance across various materials.
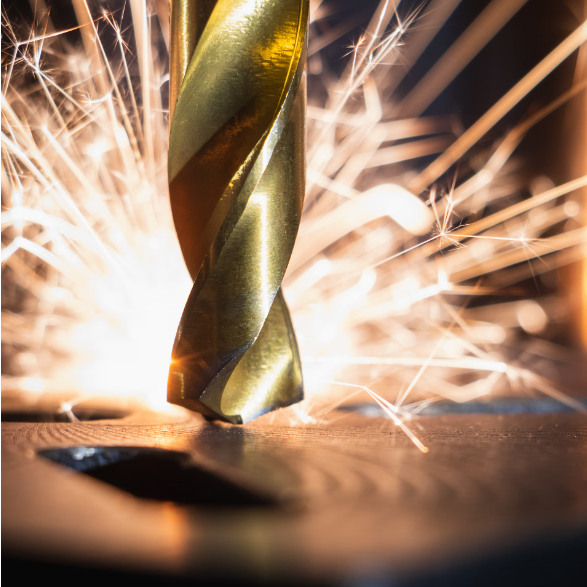
Maximize Your Cutting Efficiency: The Science Behind Tungsten Carbide Cutting Wheels
Introduction to Tungsten Carbide Cutting Wheels
In the world of precision cutting, tungsten carbide cutting wheels stand out as the premier choice for professionals and hobbyists alike. Renowned for their durability, sharpness, and efficiency, these cutting wheels are engineered to deliver superior performance across various materials. At Dongcheng, we understand the significance of quality tools in achieving optimal results, and our tungsten carbide cutting wheels are designed to meet the highest standards in the industry.
Understanding Tungsten Carbide: The Material of Choice
Tungsten carbide is a compound composed of tungsten and carbon, known for its remarkable properties. The hardness of tungsten carbide is second only to diamond, making it an ideal material for cutting applications. This section delves into the chemical and physical properties that make tungsten carbide the go-to choice for cutting wheels.
Chemical Composition and Structure
Tungsten carbide is formed through a process known as sintering, where tungsten powder is mixed with carbon and heated to high temperatures. This process results in a dense, hard material that exhibits exceptional wear resistance. The microstructure of tungsten carbide consists of fine grains that contribute to its strength and toughness.
Physical Properties
Hardness: Tungsten carbide ranks between 8.5 and 9 on the Mohs hardness scale, making it incredibly resistant to wear and tear.
Tensile Strength: The tensile strength of tungsten carbide is significantly higher than that of steel, allowing it to withstand extreme cutting pressures without deforming.
Thermal Stability: Tungsten carbide maintains its hardness even at elevated temperatures, ensuring consistent performance during prolonged cutting tasks.
The Advantages of Tungsten Carbide Cutting Wheels
Choosing tungsten carbide cutting wheels offers numerous advantages, particularly when precision and durability are paramount. Here, we outline the key benefits that set these cutting wheels apart from traditional options.
1. Superior Cutting Performance
Tungsten carbide cutting wheels provide clean, precise cuts with minimal effort. The sharp edges and robust construction allow for smooth operation, reducing the risk of chipping or breaking during use.
2. Longevity and Cost-Effectiveness
While tungsten carbide cutting wheels may have a higher initial cost compared to standard wheels, their longevity translates to significant cost savings over time. Users can expect longer service life, reducing the frequency of replacements and downtime.
3. Versatility Across Materials
Tungsten carbide cutting wheels are versatile and can handle a variety of materials, including metal, wood, plastics, and composites. This adaptability makes them suitable for multiple applications, from construction to automotive repair.
4. Reduced Heat Generation
Due to their hardness and design, tungsten carbide cutting wheels generate less heat during operation. This characteristic minimizes the risk of thermal damage to both the workpiece and the cutting tool, ensuring a longer lifespan for both.
Choosing the Right Tungsten Carbide Cutting Wheel
Selecting the appropriate tungsten carbide cutting wheel is crucial for maximizing cutting efficiency. Various factors come into play, including wheel size, grit, and intended application.
1. Wheel Size and Thickness
The size and thickness of the cutting wheel determine its cutting capacity and speed. Thicker wheels are more durable and suitable for heavy-duty applications, while thinner wheels excel in precision cutting tasks.
2. Grit Selection
Grit refers to the size of the abrasive particles on the wheel's surface. Finer grits are ideal for achieving smooth finishes, whereas coarser grits are effective for aggressive stock removal. Choosing the correct grit is essential for achieving the desired cut quality.
3. Application-Specific Features
Some tungsten carbide cutting wheels are designed with specific features tailored for particular applications. For instance, certain wheels may incorporate cooling holes to enhance airflow and reduce heat buildup, while others may have specialized coatings to improve performance on specific materials.
Best Practices for Using Tungsten Carbide Cutting Wheels
To maximize the efficiency and lifespan of tungsten carbide cutting wheels, adhering to best practices during use is essential. Here are some guidelines to follow:
1. Proper Tool Setup
Ensure that the cutting wheel is securely mounted on the tool with appropriate alignment. A misaligned wheel can lead to vibrations and uneven wear, compromising cutting efficiency.
2. Maintain Optimal Speed
Operating the cutting wheel at the recommended speed is critical. Too slow may lead to overheating, while too fast can cause excessive wear or breakage. Always consult the manufacturer's guidelines for optimal operating speeds.
3. Use the Right Pressure
Applying excessive pressure can damage the cutting wheel and the workpiece. Instead, allow the wheel to do the work by applying consistent, moderate pressure to achieve the best results.
4. Regular Maintenance
Inspect cutting wheels regularly for signs of wear or damage. Replace any wheels that show signs of excessive wear to maintain cutting efficiency and safety.
Innovations in Tungsten Carbide Cutting Wheel Technology
The cutting tool industry is continuously evolving, and recent innovations have significantly enhanced the performance of tungsten carbide cutting wheels. At Dongcheng, we stay at the forefront of these advancements to provide our customers with the best tools available.
1. Advanced Coatings
Modern tungsten carbide cutting wheels often feature advanced coatings that enhance performance. These coatings can improve wear resistance, reduce friction, and extend the life of the wheel.
2. Laser-Welded Segments
Laser welding technology allows for the creation of cutting wheels with segmented designs. These segments not only enhance cooling during operation but also improve cutting efficiency by allowing for better material removal.
3. Eco-Friendly Manufacturing
Sustainability is becoming increasingly important in manufacturing. Many companies, including Dongcheng, are adopting eco-friendly practices in producing tungsten carbide cutting wheels, minimizing environmental impact while maintaining high performance.
Conclusion
In conclusion, tungsten carbide cutting wheels are indispensable tools for anyone seeking maximum cutting efficiency. Their superior hardness, durability, and versatility make them the preferred choice for a wide range of applications. By understanding the science behind these cutting wheels and applying best practices, users can significantly enhance their cutting performance.
At Dongcheng, we are committed to providing high-quality tungsten carbide cutting wheels that meet the diverse needs of our customers. By investing in our products, you are not just purchasing a tool; you are ensuring precision, efficiency, and reliability in your cutting tasks. Embrace the power of tungsten carbide cutting wheels and experience the difference in your projects today.
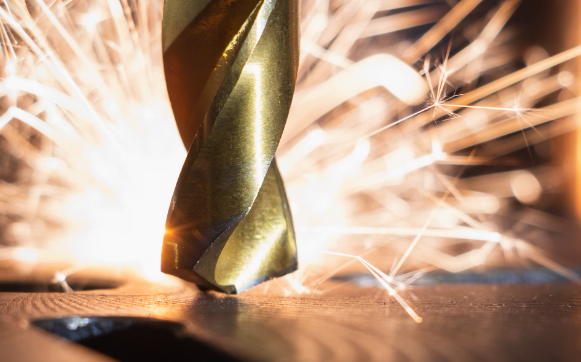